1. Wrong item location in warehouse
6. No designated location for half-picked orders
7. Fixed locations in warehouse
Picking is, as you’d expect, a major action in the order fulfillment process. Unfortunately, it’s prone to a wealth of errors that can cost you time and money if you don’t have the right workflows in place.
We’ve looked back on our experiences visiting warehouses and put together a list of the most common problems that affect order picking accuracy. This article also covers the answer to the common question: how to reduce manual picking errors.
Save the article for later and download the PDF version using the link at the bottom left.
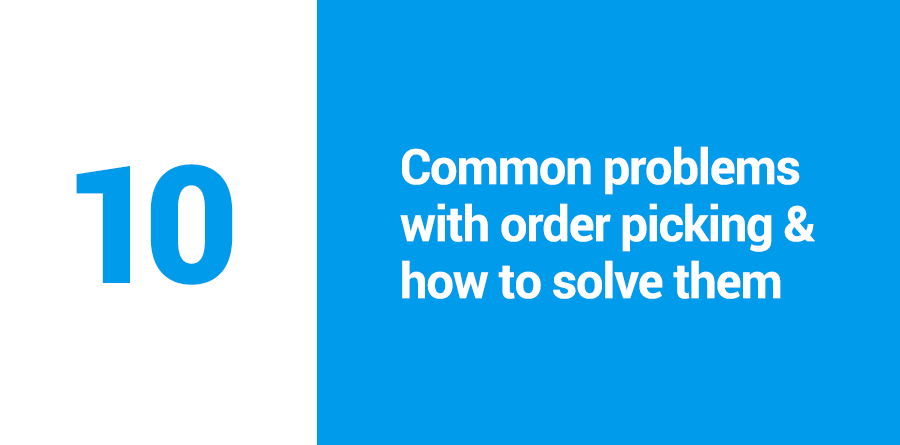
Problem 1: Wrong item location in warehouse
This occurs when a picker goes to the warehouse location to pick an order, and the correct item is not there.
Impact
If an item is not where it should be in the warehouse, this means the picker needs to spend time looking for it. This delays the order fulfillment, which can lead to an unhappy customer and negative reviews. On top of that, it also makes for a highly inefficient warehouse operation.
How to solve it
With a warehouse management system (WMS), every item is scanned into a location. This means that when a picker is looking for an item, it will always be exactly where it should be.
Problem 2: misspicks; human error
A misspick is when a picker makes a mistake, which means the wrong items or quantities are picked.
Impact
If the wrong items or quantities are picked, time is wasted at the pack bench where, hopefully, the error is noticed. If the fault is not realised, the wrong items are dispatched which will then require a refund or replacement. As well as costing money, it also paints a poor picture of your brand.
To calculate the cost of those mispicks, multiply the number of mis-shipments per week by the cost of a mis-shipment and you will see how much money is wasted. When calculating the cost of a mis-shipment, don’t forget to consider shipping costs, returns costs, labour time to re-pick, customer service work, and time spent rectifying bad online reviews.
How to solve it
Get goods-in right first time by scanning everything. Using barcode scanners in your e-commerce warehouse should make it impossible to pick the wrong item or the wrong quantity. With every incorrect pick, the scanner will create an error message, alerting the picker to their mistake.
As a final check for orders that have been picked in a batch, you may also benefit from scanning the items again at the point of dispatch to ensure you match the right items to each shipping label.
Problem 3: Paper-based picking
You are printing orders on sheets of paper and sending the pickers to manually check off their pick lists.
Impact
This kind of operation is not only a lengthy process, but it is also highly inefficient and leaves a large margin for error due to lost or unfulfilled orders. Plus, the inventory is not automatically updated when items are picked.
How to solve it
Quite simply: eliminate paper from your warehouse by using warehouse management software with a mobile app. The mobile app replaces the paper, a bit like your mobile phone replaced the handwritten letter. When you remove the room for human error, you’re in a good position to ensure that you’re able to ship every order on time, and accurately, without fail.
Problem 4: No priority when picking
All of the orders are lumped together, and there is no process for deciding which orders should be picked first.
Impact
If your orders are not prioritised, then often the most recent sales order items are picked first by default. This can mean that older orders or more important orders are neglected or delayed.
How to solve it
To solve this problem, you should find a suitable method for sorting your warehouse orders. Once you have a method in place, no priority order will be left over at the end of the day.
Problem 5: Labour-intensive picking
Your picking process heavily relies on human effort and expertise. ‘We’ve always hired more staff as we’ve grown and this can’t go on forever.’
Impact
If you have too many pickers working at the same time, you will likely be spending more money on labour than you are getting back in return. Overtime is starting to creep in and sometimes deadlines for fulfillment are missed.
How to solve it
The most efficient way to reduce the number of pickers needed for a single shift is to introduce automation into your warehouse. Automation should improve the efficiency of all your pickers, meaning that fewer of them are needed to fulfill the same amount of orders. A watches and jewellery retailer client of ours saw a 75% increase in picks per person per hour when using a WMS.
A good idea is to benchmark your picking against industry standards. 100 items per picker per hour for small e-commerce order picks is a steady benchmark. Additionally, with automated processes, you’ll be well set up to take the panic out of peak periods. With a WMS that’s easy-to-use and easy-to-train, you can get temporary staff working on the warehouse floor within minutes.
Problem 6: no designated location for half-picked orders
Workers realize partway through picking that not all of the items are currently available, and their work is wasted.
Impact
Orders that are only half-picked are generally put back if the remaining items are not available, and fulfillment is postponed. Doing this leads to unhappy customers and potential negative reviews. However, dispatching half-orders increases your overall shipping costs.
If you often find that your systems say you have an item in stock when you don’t then forget Amazon and eBay. They will take you down if you fail this fundamental test. We have known eBay Power Sellers who have lost over £100k in revenue because of this.
How to solve it
The ultimate solution is to manage your allocation properly which means orders are only half-picked if you’re happy to do a partial shipment. This is a business decision that can be set as a rule or reviewed against each order that can’t be fulfilled.
Your e-commerce platform is unlikely to give you this. Without it, half-picked and cancelled orders will be routine. With the right warehouse workflows in place, you’ll be able to improve warehouse efficiency for good.
Problem 7: fixed locations in warehouse
‘Every item has its place, except when that space is full, then it’s stored in the overstock location…wherever that is…’
Impact
Having fixed locations eliminates the potential for flexibility to allocate high-demand items closer to the pack bench when necessary. It also means that warehouse space is not fully optimised, costing money and resources.
Inefficiency here usually means replenishment is made into a bigger issue, which itself results in more manual data entry to make stock location and inventory changes. The ultimate sign this is costing you is continuous stock takes that the team rely on for accurate inventory updates.
How to solve it
Introduce a WMS that allows for dynamic locations. This will mean that you can put multiple stock keeping units (SKUs) in one location, as well as putting single SKUs in multiple locations. By doing this, you will make much better use of the space in your warehouse, save money and postpone the need to move to a larger site.
Problem 8: relying on human memory
‘My warehouse team know exactly what item is where. Contractors and temps never seem to work out.’
Impact
Time is required to train pickers on the layout of the warehouse. When peak season hits and temporary staff are taken on, the same training cannot be afforded. Having this reliance on your pickers to know where everything is will cost time and money without providing a sufficient return.
How to solve it
With a WMS, the location of every SKU should be recorded. This means that when an item needs to be picked, the location is shown on the mobile app, eliminating all need for pickers to memorise the locations. This also means that temporary pickers can start using the system immediately, without the need for involved orientation.
Problem 9: One order per pick run
Spending time walking through the warehouse to pick a single order instead of picking multiple orders along the way.
Impact
This is an inefficient process that wastes valuable time and resources. It also makes the order fulfillment longer leading to dissatisfied customers.
How to solve it
The reason that one order is generally picked in one pick run is because it is printed on a sheet of paper. However, by eliminating paper and using WMS workflows instead, pick runs can be devised in the most efficient manner, which can often mean multiple pickers pick items for one order as part of a batch run. The order is then combined at the pack bench, saving time and resources.
Here is how pick and sort to trolley flows
Problem 10: no picker accountability
You can’t trace who has picked an order, and you can’t track the progress of the order through your warehouse.
Impact
No accountability in a team is divisive, demotivating, and hard to mange. Your warehouse manager needs to be in the thick of it to have his pulse on productivity and even then he’s open to personal bias. Not having this kind of visibility means that you are unable to assess the efficiency of your staff, as well as tracking the progress of an order. This means that you can’t communicate with the customer regarding the status of their order.
How to solve it
A suitable WMS with focused e-commerce workflows should provide you will full visibility on all inventory movements, including which member of staff has performed each action. You need this focus in order to have full control over your warehouse processes and to eliminate warehouse chaos for good.
Here’s how much visibility your warehouse team could have
Ensure order picking accuracy with Peoplevox
Want to talk more about how our unbeatable ecommerce workflows will give you the ability to ship every order on time, without fail? Arrange a call with one of our specialists today.